Maintaining Seamless Data Flow with Ford at Hutchinson Paulstra
Majenta supported Hutchinson Paulstra, a leading European supplier of vibration and acoustic insulation solutions, in managing the complex data exchange requirements of their tier 1 supplier relationship with Ford Motor Company.
.webp)
faster response time in supplier-OEM communication.
data import/export accuracy within the MX+ platform.
on-time delivery of critical Ford Engine Engineering data.
reduction in time spent processing and transferring CAD data.
Project Context
As a leading European supplier of vibration and acoustic insulation solutions, Hutchinson Paulstra holds a crucial Tier 1 supplier relationship with Ford Motor Company. Working predominantly with Catia V5, Hutchinson Paulstra faced a significant challenge in managing the extensive data exchange requirements inherent in their collaboration with Ford. The high volume of data, coupled with the numerous variants of part numbers required for multiple Ford programs, placed a considerable strain on their internal resources.
Sourcing Hutchinson Paulstra on multiple concurrent programs meant Ford required frequent and large-scale data deliveries. This demand created a bottleneck in the supplier's workflow, potentially impacting project timelines and requiring a robust, scalable solution to ensure the timely and accurate exchange of critical engineering data. Maintaining efficient communication and rapid response times with Ford was also vital for a successful partnership.
.webp)
We implemented our proprietary data services to overcome these challenges.
Data Management
Majenta took responsibility for the majority of Ford Engine Engineering data flowing between Ford and Hutchinson Paulstra.
MX+ Platform
We leveraged the MX+ platform to ensure reliable and efficient data import and export.
Automated data validation
Automated data validation checks within the MX+ platform ensured data integrity and minimised errors.
Dedicated support
A dedicated Majenta support team provided ongoing assistance and expertise, ensuring a smooth and efficient data exchange process.
.webp)
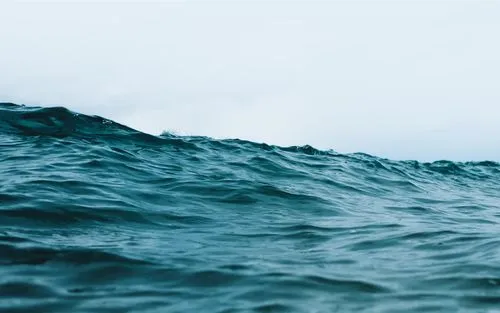
Our solution saved time while reducing costs and minimising errors.
By utilising Majenta's data services, Hutchinson Paulstra significantly reduced the time spent processing and transferring CAD data. This efficiency gain, coupled with the robust MX+ platform, ensured 100% on-time delivery of critical project data to Ford. The platform's accuracy further guaranteed reliable data exchange, contributing to a 45% improvement in communication response times between Hutchinson Paulstra and Ford.
Ultimately, our streamlined data management process allowed Hutchinson Paulstra to focus on core competencies while maintaining smooth and efficient collaboration with Ford.